Nadia's nonwoven textile: A cast silicone 2D grid with embedded electronic elements
Motivation
The purpose of my current research is to develop a tunable-stiffness material for soft robotics applications. I have been investigating a composite material made of a passive, flexible scaffold coated in an active material. Specifically, I have been looking at flexible open-cell foams coated in wax, which can be thermally activated to transition between rigid/solid states and compliant/liquid ones.
I'm using this nonwoven textile assignment as an opportunity to explore manufacturing methods for making these composites. In the past, I have used both commercially available polyurethane foams and 3D-printed flexible lattice structures for the scaffold portion of the composites. I'm interested in experimenting with various casting methods and materials to not only control the geometry of the scaffold but to also embed heating elements in it (for thermally activating the wax).
Materials & components
I'm casting a silicone (8 Shore A) 2D grid with embedded LEDs (as a proof-of-concept and place-holder for heating elements). If I can turn on the LEDs via an external battery, then I should be able to turn on embedded heating elements.
Manufacturing process
The following images show the various steps involved in 1) preparing the LEDs to be embedded in the silicone and 2) casting/molding the silicone grid.
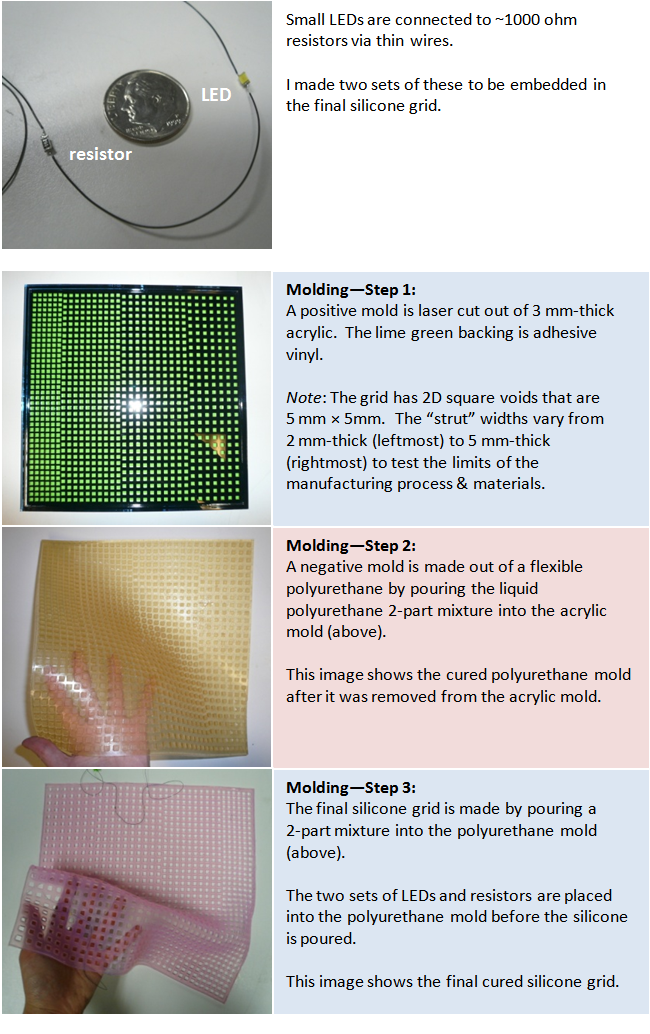
Results + Silicone dipped in wax
The following images show the final silicone grid with the embedded LEDs turned on via an external 3 V battery. Notice how flexible the silicone is.
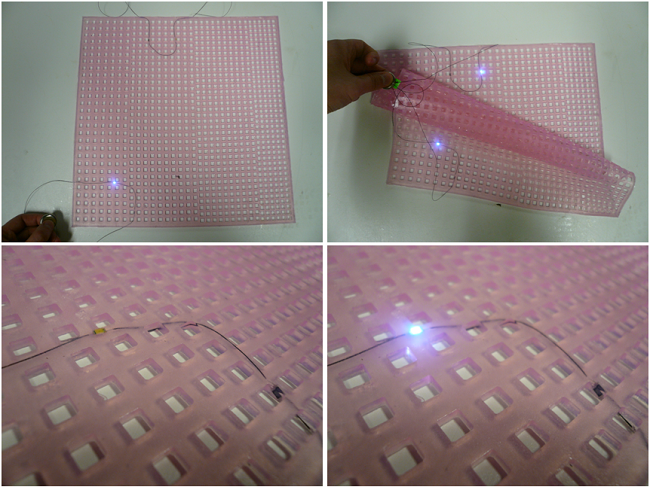
I also tested the compatibility between the silicone structure and wax by dipping the silicone grid in a molten wax bath. After coating a corner the silicone grid in wax, and while the wax was still warm and pliable, I used my hands to shape the grid and allowed it to cool in its new form, as shown below. This illustrates how well a thin layer of wax maintains the shape, even though the silicon is very flexible and would normally flop under its own weight.
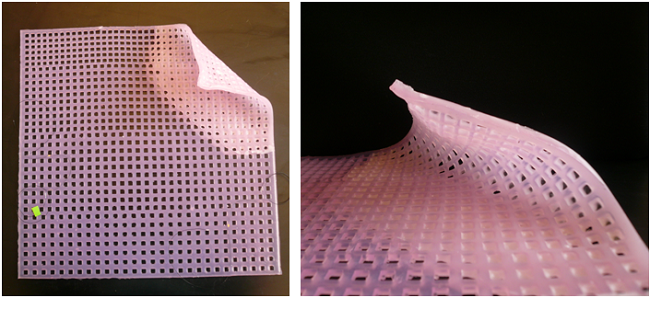
Experience
I'm really excited about the outcome of my project! Not only am I surprised by how good the quality of the cast silicone grid is, but I'm actually going to use much of what I did and learned in making materials for my research. I learned some very specific things about the manufacturing process I used that will improve future iterations of my manufactured materials:
+ It was very difficult to remove the cured polyurethane from the acrylic mold, so I should have probably used a de-molding spray (such as silicone).
+ There were many small bubbles in the cured, cast polyurethane, which most likely means that I stirred the pre-cast liquid too aggressively. I can also try putting the liquid in a vacuum chamber and/or externally vibrating the curing liquid, which is often done to remove bubbles.
+ The 2 mm-wide silicone struts in the final cast silicone grid ended up being extremely robust, so I should have been more aggressive and tried even narrower strut widths! I really didn't think it would turn out as nice as it did.
I'm also very pleased with the compatibility between the silicone structure and the wax. The next step is to embed heating elements and to see if I can locally tune the stiffness of the composite!