Electroactive Polymers
by sjacoby
Electroactive polymers (EACs), essentially speaking, are bits of rubberish stuff that changes shape when a current is applied. They’ve been around for some time and they’re not all that difficult to fabricate yourself. The paper that we read, by Petralia and Wood, explores how practically, one goes about making such a thing. Though they do their construction in a laboratory setting, the basic methods are reasonably accessibly and the materials are inexpensive.
How EACs work:
A basic dielectric EAC, like that explored in “Fabrication and analysis of dielectric-elastomer minimum-energy structures for highly-deformable soft robotic systems,” uses the electrostatic forces between two capacitive plates, to compress and deform an elastic dielectric polymer. To generate the strong deformations seen above, several thousand volts need to be applied across polymer.
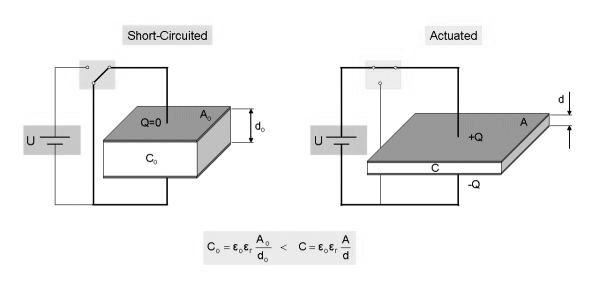
Electroactive Polymers, Un-actuated (fat) and actuated (thin)
First, just to get you excited, a teaser video, by a group out in Switzerland, that has a done a number of beautiful things with EACs:
EAP Tests EMPA 2010/08/19 from materiability on Vimeo.
Fabricating the actuators is a bit messy, but basically straightforward. The components are (mostly) inexpensive and readily available (see Supplies below). Essentially speaking, the process is as follows:
(1) Mount the polymer to a flexible frame, so that when actuated, it moved in a structured way. Otherwise it’ll just contract and wriggle like a worm on a wet sidewalk.
(2) Coat both sides of the polymer with a conductive substrate. Many examples use a kind of conductive carbon grease, that while effective, is messy. Conductive powders, etc., also work. Essentially, you’re trying to turn the polymer into a capacitor, so the conductive coating applied to its sides are the capacitive ‘plates’.
(3) Hook up each side to a high-voltage power supply or transformer.
(4) Watch the magic happen.
And a video from the same Swiss group above, showing their fabrication process. It involves some fancy equipment, but that’s really just so that they can do it in a clean way. They encapsulate the conductive powder that is brushed on the polymer, so that it doesn’t make a mess.
ShapeShift from materiability on Vimeo.
Safety
WARNING. This stuff can kill you pretty good if you don’t know what you’re doing.
To generate the electrostatic forces necessary to actuate a dielectric polymer, voltage potentials on the order of thousands of volts are used. This is not unto itself dangerous (regular static-electric sparks can be in the tens of kilovolts), but much of the equipment used to generate such voltages can easily produce unsafe current and power levels. The large potential alone means that the electricity can arc through air, damage equipment (cell phones, etc.) and give you a nice buzz even if the current is limited. And if the current levels are high enough, it can really zap you. So make sure that you’re limiting the power to something super-low, a few hundred micro-amps. Beware of any elements (capacitors, etc.) that might be storing charge.
Real Jacobs ladder from Alex on Vimeo.
Suppliers:
Most of the supplies are available through Digikey. 3M VHB acrylic tape is widely available. Digikey has it available here, as in carbon conductive grease. The greatest challenge is in safely supplying the 1-5kV required for actuating the dielectric polymers. Industrial and scientific high-voltage power supplies are available: this would probably be the easiest, most controllable, and safest way of playing in this space. Specialized high-voltage components are available from EMCO high-voltage. There are other ways of generating low-current, high-voltage, of course–one could use a Van de Graf generator or a commercial flyback transformer–a transformer typically used in conventional CRT displays. Unfortunately, such transformers can draw large currents and require some care in use. They can make
Paper:
Presentation:
Electroactive Polymers Presentation (here)